Deburring is a challenge faced by all metalworking enterprises. The size of burrs directly affects the precision, quality, and lifespan of products. Most of our products are designed for the polishing of metal parts. The principle involves using abrasive fibers with strong cutting capabilities that can rotate at high speeds to remove burrs without damaging the workpiece. Our company has designed various professional brushes suitable for parts of different shapes and materials, and we welcome inquiries from customers.
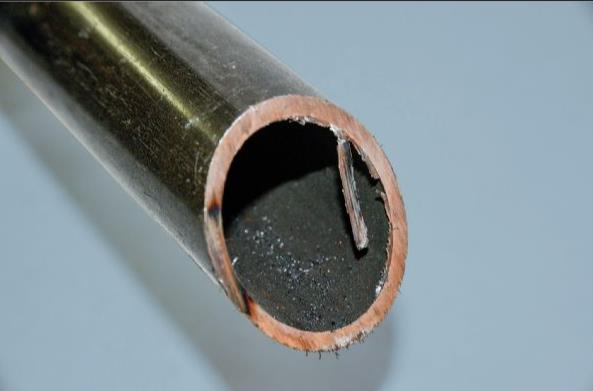
What is a deburring brush?
In the metalworking process, burrs are omnipresent. No matter how advanced the precision equipment you use, they will accompany the product. It is mainly the plastic deformation of the material, resulting in excessive metal chips at the processing edge of the processed material, especially for materials with toughness or tenacity, which are particularly prone to burrs.
Deburring with brushes involves using specialized brushes (round brushes, bowl brushes, wide brushes, edge grinding brushes, bottom grinding brushes, straight brushes, curved brushes, bent grinding hole brushes, etc.) to drive (or manually rotate) the brushes, which then abrade and deburr the workpiece. It can also chamfer, micro-finish, and polish the workpiece. This deburring method is divided into dry deburring and wet deburring. Burrs can be categorized into metal brushes and non-metal brushes. The scope of various brushes is selected based on the shape, material, burr area, and size of the parts. During deburring, the abrasive brush rotates and feeds axially, grinding and deburring the workpiece. This method is simple to operate, easy to move, cost-effective, and widely applied.
Surface Deburring and Brush Grinding
Particularly suitable for automation on production lines, it can be directly installed on CNC machining centers, lathes, robots, special-purpose machine tools, etc. It simultaneously removes burrs and polishes the processing surface, removes tool marks, improves the quality consistency of machined parts, and saves time and labor costs. It is especially suitable for processing parts with high surface treatment requirements, such as: mobile phones, notebook casings, 3C products, aluminum, magnesium alloys, stainless steel materials, etc.
Polishing brushes are used to remove burrs and polish the surface appearance. If the steel plate is sturdy, the type and characteristics of the brush bristles need to be determined according to the different requirements and the appearance of the bristles. For electroplating and polishing, the ideal bristle should be bronze wire. If the appearance is treated for rust prevention and deburring, the hardness of the accepted wire can be better, which is usually the case for metal materials.