A scraper blade is made from engineered rubber with a special wear-resistant and anti-cracking formula. The shape of the scraper blade varies depending on the customer’s rail and the shape of the rail to be protected. The main purpose of installing a scraper blade is to provide effective protection for the rails of CNC machine tools.
When CNC machine tools are cutting automotive or aerospace metal parts, the spindle moves along the rail, and metal chips are highly likely to splash into the gaps between the rail and the sliding block. If a scraper blade is installed above the rail, it can effectively protect the rail from these chips.
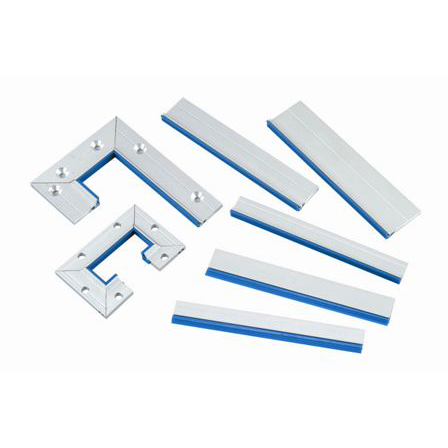
What Types of Scraper Blades Are There?
When CNC machine tools are cutting automotive or aerospace parts, metal chips splash into the gaps of the rails. In this case, a scraper blade must be installed between the mechanism above the rail and the rail itself to provide protection. Since every CNC machine has moving axes such as X, Y, Z, and even A and B, these movements are driven by the rails and mechanisms. Therefore, almost every CNC machine requires many scraper blades. A common issue when ordering new scraper blades or replacing old ones is the variety of specifications, which may not be customizable. However, scraper blades can be categorized based on the shape of the rail, manufacturing method, and materials used, as detailed below.
Category 1: Rail Shape
- Straight Type
General CNC machine tools or traditional machine tools often use scraper blades. When the scraper blade’s purpose is to clean the platform, a straight type aluminum scraper blade is commonly used. - Dovetail Type
The most commonly used rail type for CNC machines and general lathes is the dovetail type. For dovetail rails, scraper blades must be custom-made to match the dovetail shape to effectively protect the rail. These are also referred to as new-type scraper blades.
Category 2: Scraper Blade Manufacturing Method
- Molded Scraper Blades
Molded scraper blades are produced using molds. If the scraper blades have fixed specifications and a high quantity, they can be molded to help control costs. We can also incorporate sheet metal into the molding process to enhance the overall structural strength of the scraper blade. - Aluminum Strip Scraper Blades
Aluminum strip scraper blades are made from aluminum material and PU scraper strips, typically used for cleaning the platform of CNC machine tools. Their key feature is a simple structure that is easy to install. - New-Type Scraper Blades
New-type scraper blades are custom-made according to the customer’s rail shape. Their design can be fully customized. Common applications include lathes, dovetail rails, and the gaps between the X-axis sliding table of CNC machine tools.
Three Key Points to Consider for Scraper Blades
- Point 1: Fit Degree
When installing scraper blades, it is essential to pay attention to the fit between the scraper tongue and the bed. For applications requiring long scraper tongues, it is recommended to process the fixed sheet metal with a long hole to facilitate vertical adjustments. - Point 2: Regular Replacement
The recommended replacement cycle for scraper blades is every 5-10 years after installation. Regular replacement is advised to ensure the CNC machine, lathe, and other equipment maintain optimal accuracy and rail condition. - Point 3: Custom Scraper Blades
Older machines often face the issue of scraper blade production being discontinued. If you can provide cross-sectional dimensions, quantities, or samples, we can help evaluate the feasibility of producing custom scraper blades.